Automated Weighing and Labeling for the Meat Industry

Using automation in weighing and labeling turned into an essential practice for most successful food industry businesses in North America. The meat industry is NO exception.
Meat Industry businesses have long become aware of the benefits of automated weighing and labeling for increasing profitability and minimizing compliance risks. These risks can lead up to scary scenarios like a food recall or consumer complaints when manual practices are followed.
What is an Automated Weighing & Labeling Solution?
Automated Weighing and Labeling Solutions are highly accurate, efficient, and streamlined solutions that enhance a processor’s ability to produce at higher volumes with consistency.
An automated weighing and labeling solution improves a food processor’s operation by removing the manual aspect of product weighing and labeling. This reduces human error and increases production throughput. Automated in-motion Solutions can offer advanced features such as inbound product identification used to identify mixed products prior to weighing. Automated weight and data capture, outbound label verification, reject management, and product sortation.
Problems of a Manual Weighing & Labeling Solution in the Meat Industry
An automated weighing and labeling Solution is a long-term investment a processor can make, that yields great returns throughout their production process. The typical places a processor sees ROI is:
- Increased throughput
- Ability to expand into higher-volume markets
- Reduced labeling errors
- Reduced human dependency
- Combining multiple lines into a single line
A typical manual case weighing line has an average throughput of 10-12 boxes per minute depending on the operator. An automated case weighing, and labeling line has an average throughput of 25 boxes per minute. The automated line has twice the throughput capabilities that a manual Solution has. While the automated weighing and labeling solution is costlier upfront than a manual system, the ROI is in the long-term volume of products generated. For example, instead of paying an operator to sit at each line to weigh and label a product while paying them $40,000 a year, this can be invested into an automated weighing and label solution. In 3 years at that salary rate, the automated solution is paid for, and the human capital can be reallocated which in turn saves money.
As a processor begins to expand their operations, demand inevitably will overwhelm a manual system’s ability. Smaller processors trying to grow the organization and expand their outreach into new markets have their sights set on supplying some of the largest food distributors in North America.
To be able to supply to these large-scale distributors, certain requirements need to be met by the supplier. One of the most important requirements, is the ability to produce in high volumes. A manual weigh and label process can only take a processor so far in terms of throughput. It would not be able to meet the demands of higher volume markets. An automated weigh and label solution has the ability to consistently and accurately meet volume output goals.
Aside from being able to supply enough volume, large-scale distributors also have a rigid process for their label requirements. Labels need to be standardized GS1-28 barcoded labels, that are placed in the correct area of the box with very little variance deviation. This is due to their strategy of scanning the same area of the pallet which goes into inventory as quickly and efficiently as possible. Automated weighing and labeling Solutions can weigh and label the product in the exact same spot consistently and accurately while adhering to the specific location for label application. This verifies to a large-scale distributor that you have Solutions in place to adhere to rigid requirements and can supply them.
Another major ROI for a processor when implementing an automated weighing and labeling system is the reduced dependency on human capital. A business can face human capital risks such as:
- Labour shortages due to external market events
- Employee retention
- Employee training
Processors can be faced with an evolving labour problem due to the COVID-19 pandemic, inflation, and other external problems. Employees could leave the facility and look for other work. Recent events in the food processing industry have been showing employers offering incentive signing bonuses to attract new talent. However, incentive programs have met minimal success. Food processors who have managed to withstand external pressures on their labour pool have also had issues with employee retention. This leaves a processor with a constant issue of hiring, training, and dealing with turnover rates. An automated weigh and label Solution can reallocate human capital from the weighing and labeling process to other areas within the plant, while the automated solution can now handle those functions.
Another major benefit of an automated weighing and labeling Solution is consolidating multiple lines into a single line. A typical processor will have multiple lines based on various products being produced. Instead of having two or three stand-alone manual lines, a processor can save real estate by joining lines. This will also reduce the number of operators for their packaging operation.
What are the key components of an automated food labeling solution?
Automated Weighing and Labeling Solutions are multi-component solutions. These include:
- Print and Apply Solutions
- Conveyor Scales
- Inbound & Outbound Scanning
- Box Indexer
- Sortation
Print and Apply Systems
Print and Apply Solutions are engineered and designed for a variety of environments to operate in such as wet, dry, humid, washdown intensive, etc. Some of the different component structures for a Print and Apply Solution are:
- Pneumatic Powered
- Electric Powered
Pneumatic powered applicators are typically used in a stable environment, that is not wet, harsh, humid, etc. Designed to meet the demanding needs of manufacturing, warehouse, distribution, fulfillment, or third-party logistics (3PL) environments. Utilizing zero-waste pneumatics in order to consistently and accurately apply a label(s) to an in-motion case on a conveyor line. Pneumatic applicators are a great starting point for most processors to meet volume, speed, and accuracy requirements. However, in wet, washdown, or harsh environments, pneumatic applicators cannot operate as efficiently. This is because a cold environment impedes the compressed air flow, causing low pressure and reduces the print and apply Solutions’ effectiveness. This is generally where most processors will look to electric print and apply Solutions.
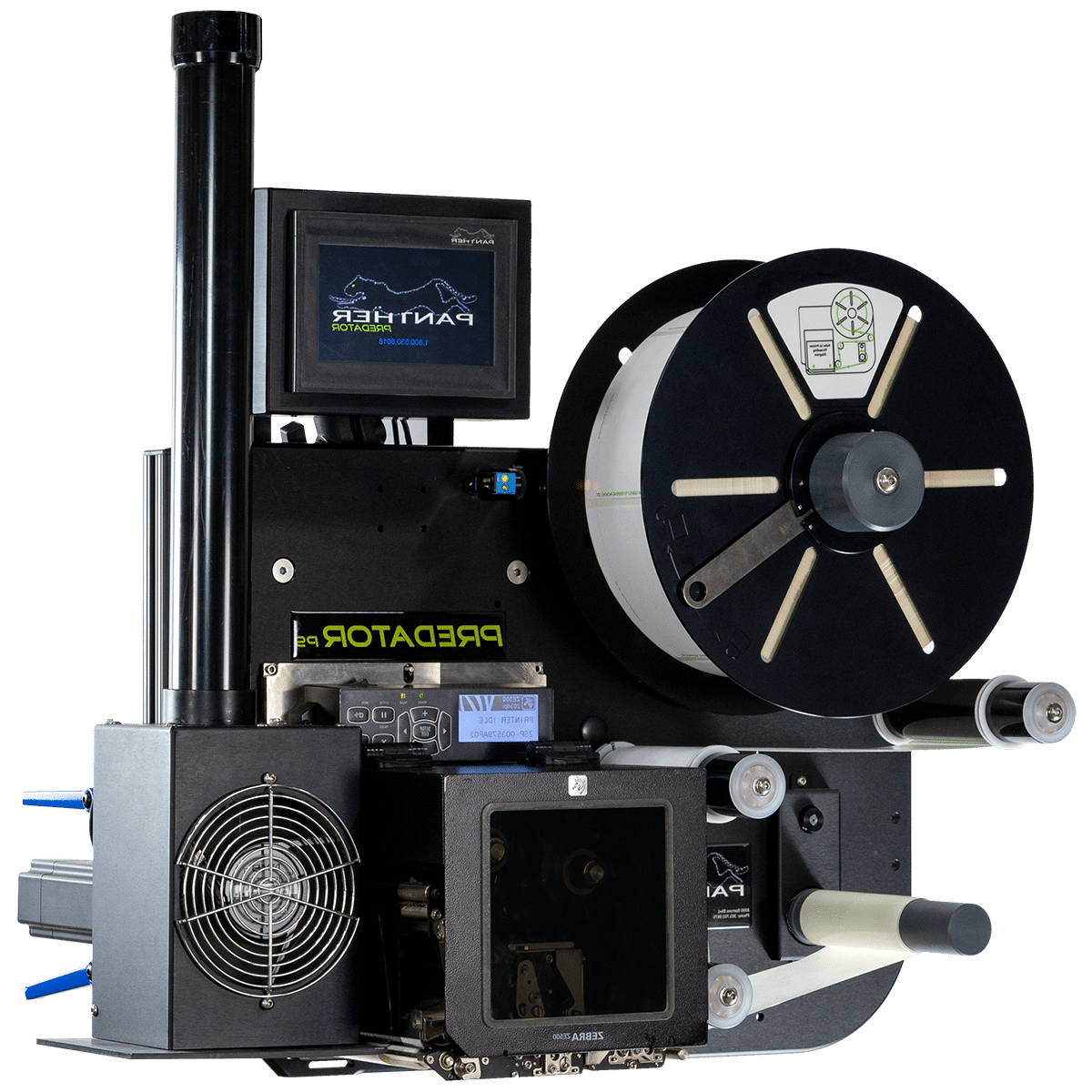
Electric print and apply Solutions are all-electric label automation Solutions that are durable, reliable, and a consistent option for exceptional print and apply performance. Electric applicators are a great consideration for a processor whose operations are fast-moving, high volume, and have harsher environments. While electric print and apply Solutions are typically costlier than pneumatic, they come with a slew of benefits. For example, the system’s adaptive applicator automatically adjusts to carton heights while items are in motion, delivering exceptional capabilities to support complex supply chain and material handling operations. Electric print and apply Solutions are a fantastic choice for a processor who has sufficient capital to spend on long-term investments that will drive the bottom line. Print and apply Solutions are one component of an automated weighing and labeling solution. They work in tandem with conveyor scale Solutions.
Conveyor Scales
Conveyor scales offer incredible in-motion weighing accuracy with high-speed capabilities. The scale is fitted with a smooth belt-driven design to minimize vibrations during weighing. They can be designed to ensure the scale fits within your existing processes and meets your exact needs. Constructed for harsh, washdown environments they are a great addition when a processor is moving towards an automated process within their facility to accommodate the higher volume.
Conveyor scales are typically fitted between an infeed conveyor and where the product is flowing, and an outbound conveyor towards a palletizing section. A conveyor scale works in tandem with a print and apply system. Photo eyes are placed before and after the conveyor scale which triggers the weighing process. Once the box is weighed, another photo-eye triggers the print and apply solution to automatically label the product after the weighment. Another addition a processor can make to a conveyor scale solution, is a box indexer.
Box Indexers
Box indexers are a great addition to an existing conveyor Solution that can be added. The box indexer ensures that there is consistent box spacing. It enables down-line printers, checkweighers, conveyor scales, and scanners to function within specifications that a processor can determine. A box indexer prevents an overflow of products that can cause production downtime.
Most processors typically have a multitude of different products that they are producing and selling. Scanning is another aspect of an automated weighing and labeling system, that further enhances the solution through product verification and tracking. Inbound scanning determines the different products traveling down the conveyor. This allows the software application to select the right label format for the product. Outbound scanning is a verification that the product being weighed has the correct label on it. A diverter can also be added to the solution if a product does not fit within set parameters or has an incorrect label, so a box can be reworked correctly. Inbound and Outbound scanning also provides a clear picture of where your product is throughout production in real-time.
With various products, a processor can have multiple products on a single conveyor line. Sortation is another addition that can be added to enhance an automated weighing and labeling solution. A processor may have various sortation lines for different products, which then have their own respective palletizing area. Having a sortation Solution is a major benefit as it reduces the need to sort through multiple products on a single line and increases overall line efficiency and throughput.
The major overarching benefit to an automated weighing and labeling system is the minimal human interaction. Operators will still need to be present in the event of an error such as a rejected product that requires them to manually restart the line. However, human capital can be reallocated from the weighing and labeling process to other areas within the plant.
How can Carlisle Technology help?
Over the past 30+ years, Carlisle Technology has earned a solid reputation for supplying the very best integrated case weighing and labeling solutions in North America. Carlisle Technology’s Automated Case Weighing and Labeling Solution integrates the industry’s most robust hardware solutions with our configurable software. We partner with the very best manufacturers to provide the best of breed high accuracy in-motion carton scales, product indexers, infeed conveyors, and print and apply Solutions.
If you have any questions on food weighing and labeling solutions, we would love to hear from you. Give us a call and our experts can help you select the correct weighing and labeling solution and guide you through the implementation process.
Written by: Joe O’Keefe, Account Manager – Carlisle Technology
Sign Up for Our Newsletter!
Receive updates on products, customer stories, and giveaways!
By submitting this form, you are consenting to receive marketing emails from: . You can revoke your consent to receive emails at any time by using the SafeUnsubscribe® link, found at the bottom of every email. Emails are serviced by Constant Contact